From Posture Recognition to Material Innovation
After completing the Seating – Posture Recognition System project, I started exploring ways to reduce the cost and complexity of integrating sensors into car seats. Instead of embedding traditional pressure sensors into foam, I researched the potential of conductive, sewable threads to weave them directly into the seat structure or embed them within the foam itself. The goal was to create a durable, flexible, and cost-efficient sensing solution that could withstand repeated stress cycles.
Conductive Thread and Material Science Challenges
The key challenge in this project was material durability. Unlike conventional pressure sensors, which have a proven track record, conductive threads faced significant issues during stretch resistance tests. Under repeated seating cycles, the threads exhibited rapid degradation, with conductivity loss occurring far sooner than expected.
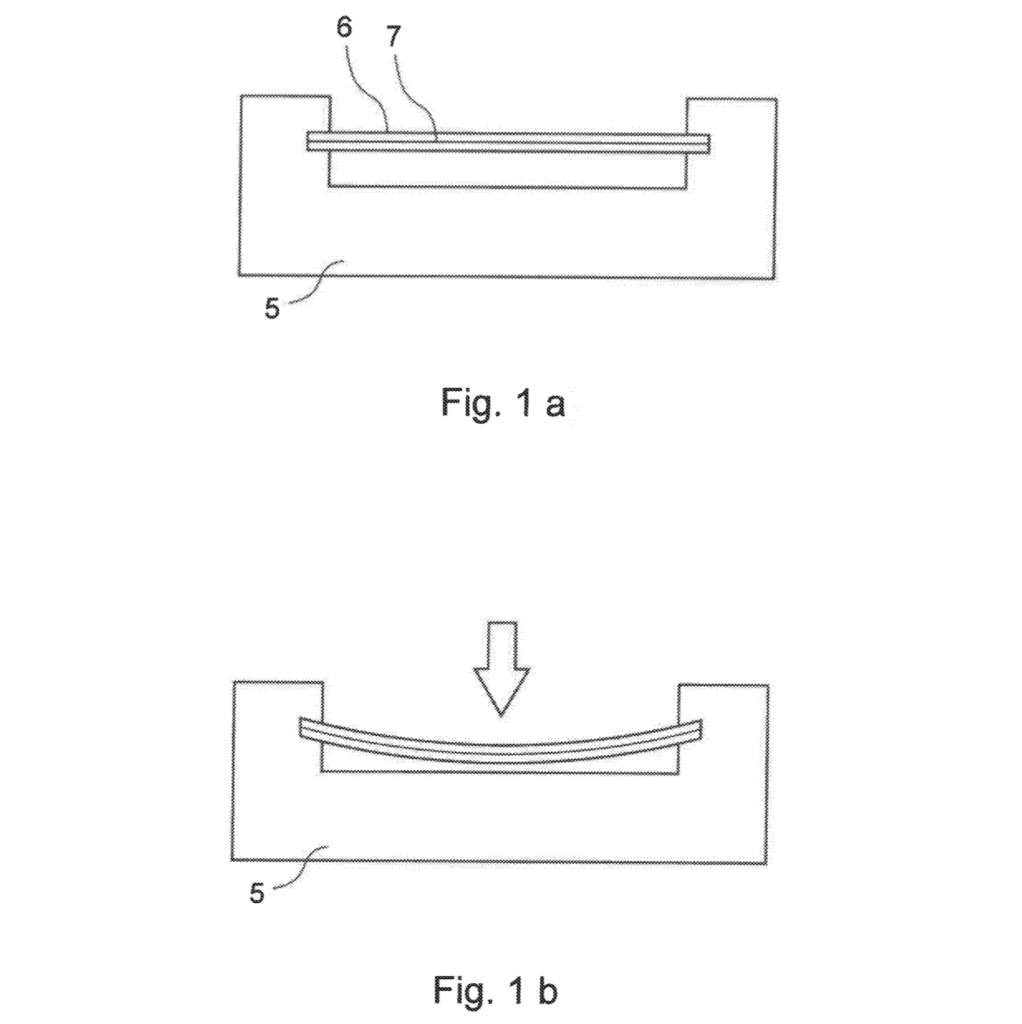
I conducted multiple tests to evaluate their viability:
- Conductivity tests, measuring resistance fluctuations over extended load applications.
- Durability assessments, analyzing breakdown points due to mechanical stretching and compression.
- Comparison with traditional pressure sensors, measuring accuracy, signal reliability, and long-term performance.
Unfortunately, the results showed that conductive textile elements suffered from high failure rates under heavy loads. Unlike pressure sensors, which offer stable, repeatable measurements, the conductive threads showed inconsistent readings and frequent breakage, making them unsuitable for real-world automotive applications.
Prototype Development and Arduino Integration
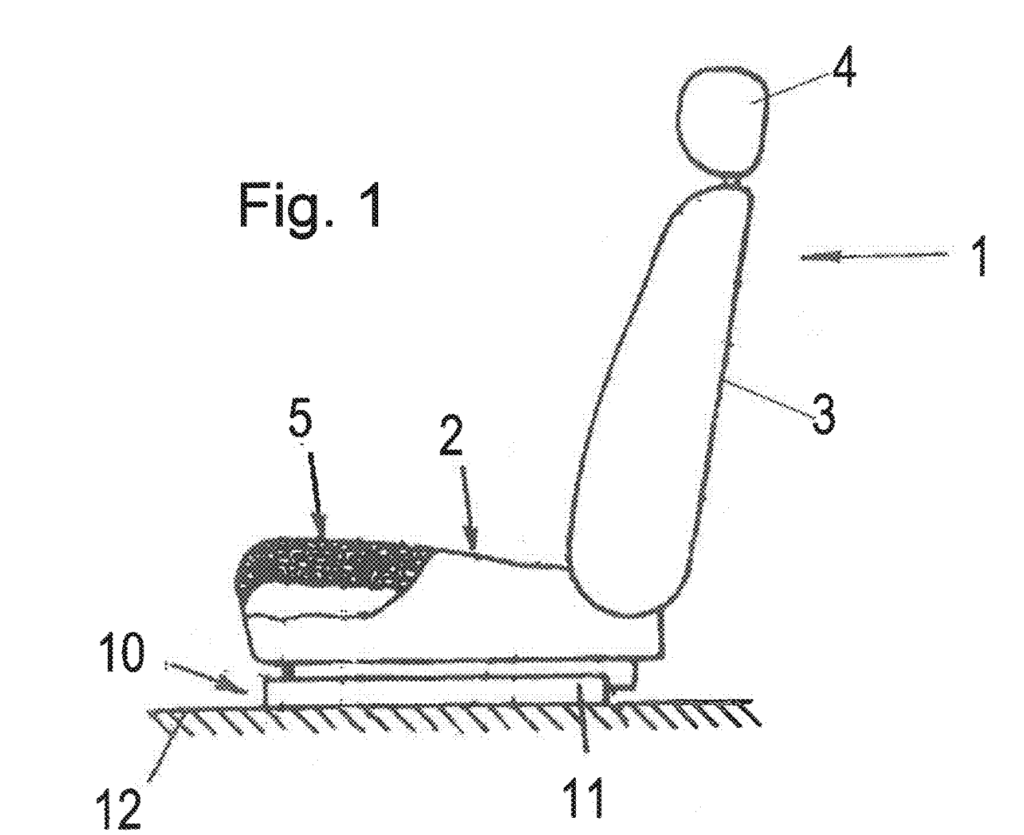
To validate the idea, I developed a prototype using Arduino for data processing. While I was able to:
- Interface the conductive threads with a real-time monitoring system.
- Implement basic signal filtering to reduce noise.
- Capture force distribution changes dynamically.
The inconsistencies in conductivity meant that the filtering process became increasingly complex, requiring manual recalibration after relatively few cycles. The sensor system failed to provide the stability needed for practical use.
Performance Analysis and Repeatability
Extensive repeatability tests confirmed the limitations of this approach:
- The conductive sensor array degraded after just a few thousand load cycles, far below the expected endurance threshold.
- Signal reliability decreased over time, leading to erratic readings.
- Response times were worse than traditional pressure sensors, and the fragile nature of the threads meant frequent replacements were necessary.
Lessons Learned and Next Steps
This project taught me some important lessons about material science and real-world application constraints:
- Conductive threads are not a direct replacement for traditional pressure sensors – they lack the durability needed for automotive use.
- Mechanical stress is a major factor – any flexible sensor must endure repeated compression without losing functionality.
- Cost-saving ideas must also prioritize reliability – while textile-integrated sensors seemed like a lower-cost alternative, the high failure rate negated any financial benefits.
Going forward, hybrid solutions need to be explored which combine traditional pressure sensors and smart textiles, ensuring both durability and cost-effectiveness. While this attempt didn’t yield the expected results, it was an invaluable learning experience in materials engineering and sensor integration.